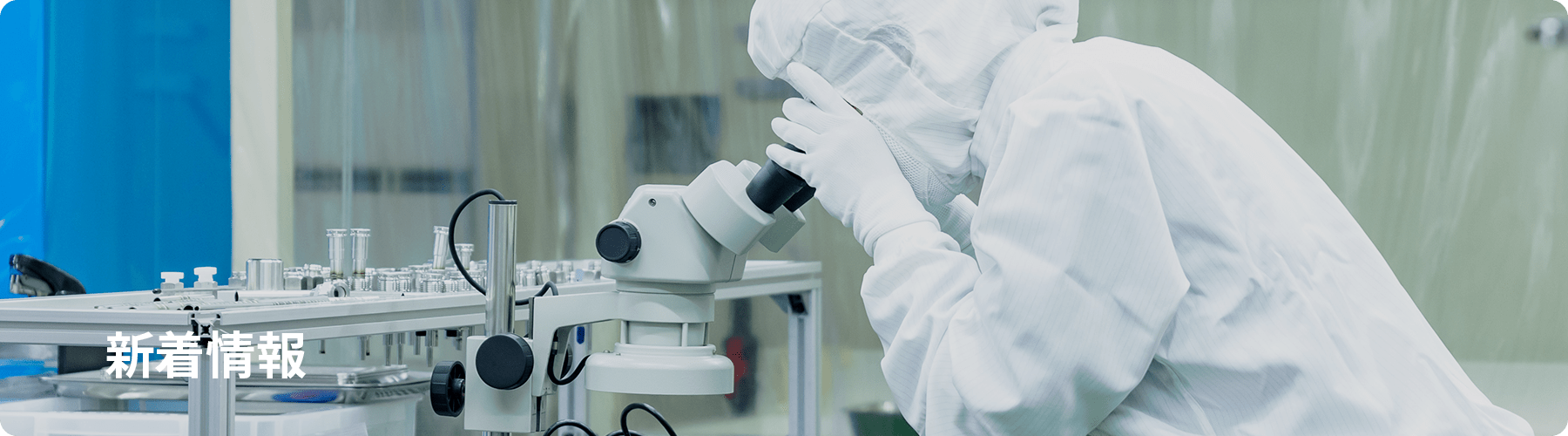
皆さんこんにちは!
株式会社Tnor、更新担当です。
さて
~工程設計~
ということで、精密洗浄における工程設計の基本構成から、各ステップでの留意点、最適化の方法までを実務レベルで詳しく解説します
精密機器産業において、「洗浄工程」は単なる前処理工程ではなく、製品性能そのものを左右するコア工程のひとつです。特に半導体、光学、医療機器、航空宇宙といった業界では、ナノレベルの粒子や化学残留物が製品に致命的な欠陥を与える可能性があるため、科学的・統計的な裏付けをもった工程設計(プロセス設計)が必要不可欠です。
。
まず、精密洗浄の工程設計とは何を意味するのかを明確にします。
安定した清浄度の達成(再現性)
製品へのダメージ回避(表面変化、腐食、変形など)
作業効率・コスト最適化
トレーサビリティと品質保証の確立
精密機器向け洗浄では、以下のような多段階の工程が採用されることが一般的です:
予備洗浄(プレウォッシュ)
└ 大まかな油分や粉塵の除去。多くは中性洗剤を使用。
本洗浄(メインウォッシュ)
└ 超音波洗浄や薬品洗浄を含む工程。粒子、イオン、有機物を徹底除去。
リンス(純水洗浄)
└ 超純水を使って洗浄薬品や汚染物を完全にすすぐ。
乾燥(ドライ工程)
└ クリーンオーブン、IPAディスプレイスメント、真空乾燥など。
検査・評価
└ 粒子数、TOC、残留イオン、外観などの評価による工程の妥当性確認。
材質によって、使える薬品や超音波出力が大きく変わります。
アルミ → 酸性薬品NG、腐食リスクあり
ステンレス → 塩素系薬品は応力腐食のリスク
樹脂 → 有機溶剤により膨潤・変形の恐れ
→ 材質ごとのSDS適合チェックと事前テストが必須
洗浄後に求められるスペックを設計時に明確化します。
指標 | 例 |
---|---|
粒子数 | 0.5μm未満の粒子が100個以下 |
有機物残留 | TOC 5ppb以下 |
金属イオン残留 | Na⁺、Cl⁻など 1ppb以下 |
表面粗さ | Ra 0.05μm以下維持 |
→ 仕様から逆算して洗浄方法・時間・濃度を決定
物理的方法:超音波洗浄、スプレー洗浄、真空洗浄
化学的方法:酸洗、中性洗剤、有機溶剤、キレート剤など
精密分野では、これらのハイブリッド方式(物理+化学)が主流です。
例
ステンレス微細部品の洗浄
→ 中性洗剤+40kHzの超音波洗浄(10分)+超純水リンス(5分)+IPA乾燥
洗浄工程そのものがクリーンルーム内で行われることも多く、その設計も重要です。
クリーン度クラス(ISO 14644-1に準拠)
静電気管理(ESD対応)
温度・湿度・空気流量のコントロール
作業員のPPEや教育訓練体制
洗浄直後の乾燥が不十分だと、水滴によるマイクロスケールのウォータースポットや腐食を引き起こします。
IPAディスプレイスメント乾燥:気化熱で素早く乾燥
クリーンオーブン乾燥:低温+HEPAフィルター対応
真空乾燥:表面残留水分ゼロを目指す高精度法
また、洗浄後はすぐにクリーンパック(ナイロン/アルミ袋+窒素置換)で密封保管するのが望ましいです。
精密洗浄工程では、以下のような品質管理手法を活用した工程設計が推奨されます。
DOE(実験計画法):温度・時間・濃度などを統計的に組み合わせ最適条件を決定
FMEA(故障モード影響分析):洗浄工程でのリスク要因を洗い出し、対策を講じる
SPC(統計的工程管理):洗浄後の粒子数やTOCを定量管理し、異常の早期発見に活用
精密洗浄は、もはや「洗う」という単純作業ではなく、プロセスエンジニアリングそのものです。正しく工程を設計・文書化し、常に管理・改善を行うことで、製品の信頼性と市場競争力を飛躍的に高めることができます。
製品トラブルが発生したとき
顧客仕様が変わったとき
新しい洗浄薬品や設備を導入したとき
洗浄品質のばらつきが見られるとき
今の工程が本当に最適なのか、定期的な「工程レビュー」も品質維持のカギです。
お問い合わせはお気軽に♪
皆さんこんにちは!
株式会社Tnor、更新担当です。
さて
~確認事項~
ということで、精密機器洗浄に携わる現場で実施すべき高度な事前確認事項を、5つの視点から詳しく解説します。
精密機器分野における産業洗浄は、他業種と比べて格段に高い精度と管理レベルが求められます。半導体、医療機器、航空部品、光学機器などの分野では、わずかな粒子・汚染が致命的な欠陥や不良を引き起こす可能性があるため、洗浄工程は製品の品質保証において非常に重要です。
そのため、作業前の「事前確認」を徹底することが、安全性と製品品質を両立させる鍵となります。
精密機器では、部品の材質やコーティングが非常に繊細です。まずは以下の点を詳細に確認する必要があります:
材質の種類:アルミニウム、チタン、セラミック、ステンレス、特殊樹脂など
表面処理の有無:酸化膜、陽極酸化、メッキ、樹脂コートなど
耐薬品性・耐熱性の確認:薬品や温水の使用が想定される場合は必須
表面を傷つけたり、コーティングを剥がすような洗浄方法を避けるため、図面・仕様書の事前取得と確認が重要です。
精密機器分野では、「洗浄した」だけでは不十分です。どのレベルまで清浄にするか、クリーンネス基準を正確に把握しましょう。
パーティクル(粒子)サイズの基準:例)0.3μm未満の粒子残留なし
油脂・有機物の残留許容範囲:TOC(全有機炭素)基準など
イオンクリーニング基準:金属イオンや塩素イオンの残留管理
洗浄後の検査方法(光学顕微鏡、FTIR、白濁試験など)とあわせて、顧客と仕様を事前にすり合わせる必要があります。
精密部品の洗浄では、薬品や超音波の使用条件が極めて限定されることがあります。
中性洗剤や超純水の使用が前提のケースも多い
超音波洗浄の周波数や出力の設定確認(共振による破損防止)
真空洗浄・気化洗浄など特殊工法の指定がある場合も
使用薬品のSDSの確認と、保管・希釈方法の明文化
特に有機溶剤(IPA、アセトンなど)を使用する場合は、防爆設備や換気の有無も確認しましょう。
精密機器洗浄では、洗浄環境自体のクリーン度も重要です。以下の環境条件を作業前にチェックしましょう。
クラス100~100,000のクリーンルームレベルの確認
エアシャワー・粘着マットなどの異物管理設備の有無
作業員の無塵服・手袋・マスク・靴カバーの着用状況
静電気管理(ESD対策)が必要な場合の装備確認
搬入前後の製品保管方法(クリーンパック、真空包装など)も事前に確認し、不純物再付着のリスクを防ぎます。
精密分野では、「誰が」「いつ」「どのように」洗浄したかを追跡可能にする必要があります。
作業員の記録、使用薬品のロットNo、洗浄条件のログ化
洗浄後の乾燥・検査記録の保管
顧客提出用の清浄度検査結果の帳票準備
自社でのISO9001やISO13485の運用体制がある場合は、それに準じた文書管理を徹底します。
精密機器の洗浄では、「見た目がきれい」では不十分であり、数μm以下の異物・残留物までコントロールすることが求められます。
それを実現するためには、事前確認を徹底してリスクを最小限に抑えるプロセス設計が不可欠です。
項目 | チェック内容 |
---|---|
対象物 | 材質、コーティング、寸法 |
清浄度 | パーティクル基準、TOC、イオン残留 |
洗浄法 | 使用薬品、機器の設定、手順 |
環境 | クリーンルーム条件、作業者PPE |
管理 | 記録の保管・提出フォーマット |
作業前の5分の確認が、製品の不具合ゼロ・顧客信頼の向上に繋がります。ぜひ自社の手順書や教育マニュアルに取り入れてください。
お問い合わせはお気軽に♪